
- Key Takeaways
- OSHA Requirements for Recording Work-Related Incidents
- Conducting Thorough Woodworking Incident Investigations
- Best Practices for Incident Reporting
- Corrective Actions to Prevent Woodworking Incidents
- Key Elements of an Effective Safety Program
- Sharing Lessons Learned From Incidents
- FAQs
- Call to Action
Key Takeaways
- OSHA recordable incidents include injuries requiring medical treatment, days away from work, restricted duty, loss of consciousness, or death.
- A thorough incident investigation determines root causes like unsafe equipment, lack of training, improper PPE, fatigue, or complacency.
- Implementing corrective actions and sharing lessons learned help avoid repeat incidents.
OSHA Requirements for Recording Work-Related Incidents
The Occupational Safety and Health Administration (OSHA) mandates that employers track and report work-related injuries and illnesses on the OSHA 300 log.
OSHA recordable incidents in woodworking shops include:
- Injuries requiring medical treatment beyond first aid
- Lost time incidents resulting in days away from work
- Restricted duty limiting normal work tasks
- Shock, loss of consciousness, or death
- Cuts and lacerations disabling for one or more days
Minor first-aid level injuries do not require formal reporting. However, even these should get documented internally to identify problem areas.
OSHA Reporting Timeframes and Fines
Employers must report work-related fatalities within 8 hours and inpatient hospitalizations, amputations, and loss of an eye within 24 hours. Failure to report significant incidents can result in OSHA fines up to $134,937 per violation.
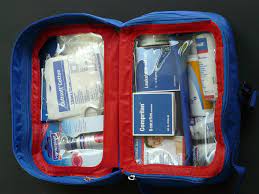
Conducting Thorough Woodworking Incident Investigations
Every recordable woodworking accident warrants a formal incident investigation to uncover contributing factors and prevent recurrence.
Investigations should involve the injured worker’s supervisor, safety committee members, subject matter experts, and witnesses.
- Interview the injured employee and witnesses separately. Avoid blame and encourage open dialogue.
- Document details through photographs, measurements, video footage, written statements, injury logs, and medical reports.
- Determine the sequence of events leading up to the incident. Build a timeline noting equipment, processes, and behaviors involved.
- Identify root causes like improper guarding, lack of training, complacency, fatigue, problematic SOPs, and other underlying safety culture issues.
- recommend targeted corrective actions addressing each root cause through engineering solutions, updated policies, refreshed training, accountability review, etc.
Present findings to management and implement changes to prevent similar future incidents.
Best Practices for Incident Reporting
Every woodshop should have standardized reporting procedures for work-related injuries, near misses, property damage, fires, spills, and health exposures.
- Post instructions for emergency response contacts, coordinates, protocols near common work areas.
- Maintain incident report forms with sections on reporting party, name/department of injured, incident type, date/time, exact location, witnesses, description of events, apparent injuries, corrective actions taken.
- Document near misses too – these present opportunities to improve safety before actual harm occurs.
- Provide training to employees on importance and process of reporting all incidents even if no injury or minimal damage occurred.
- Remove fear of reprisal for minor mistakes and reward speaking up about hazards or close calls.
Corrective Actions to Prevent Woodworking Incidents
Every incident investigation should outline corrective actions targeting root causes. For example:
- Install machine guarding
- Improve ventilation and dust collection
- Refresh PPE policies and training
- Review proper use of tools/machines
- Update safety rules and disciplinary policy
- Increase supervision and audits
- Fix hazards like cluttered aisles, slippery floors
- Enhance preventative maintenance
- Provide job rotation, ergonomics review, fatigue breaks
Track progress to ensure adequate resources target each action item and full completion by assigned personnel. Analyze success through lead and lag indicators like safer behavior observations, reduced incidents, lower workers’ compensation costs within 6-12 months.
Key Elements of an Effective Safety Program
Robust safety programs integrate strong leadership, engaged frontline workers, anonymized reporting, and centralized tracking to drive continuous improvement.
Core elements include:
- Written policies and procedures set clear expectations “Safety requirements in Employee Handbook“
- Baseline risk assessments identify hazards for priority mitigation
- Inspection checklists verify safe conditions periodically
- Anonymous safety reporting via suggestion boxes or online forms
- Centralized collection of safety metrics like near miss and injury rates
- Safety training on company policies, job-specific hazards, proper precautions
- Safety incentives rewarding safe behaviors
- Corrective action tracking to guarantee fixes “Online action item tracker“
- Program audits every 3 years assess effectiveness
Sharing Lessons Learned From Incidents
Analyzing injury causes and communicating corrective actions shop-wide prevents repeat issues.
- Present investigation findings at safety committee meetings
- Discuss incidents at startup tailgate safety talks
- Email recap of serious incidents and improvements to all shop employees
- Publish preventative solutions on the company intranet
- Feature health and safety in company news
- Feature health and safety in company newsletters or social media
- Develop new safety rules and best practices building on past experiences “Limit jewelry and loose hair around machinery”
Open communication and transparency around incidents improve reporting, make safety personal, and build an interdependent culture dedicated to protecting one another.
FAQs
What are OSHA recordable incidents?
OSHA recordable injuries include those needing medical treatment, restricted work, time away from work, or resulting in loss of consciousness or death. These get logged on the annual 300 log.
What are the reporting timeframes for serious incidents?
Fatalities must report to OSHA within 8 hours. Overnight hospitalizations for medical treatment, amputations, or loss of an eye necessitate filing a report within 24 hours.
Should minor first aid cases get documented?
While not OSHA recordable, even minor scratches or bruises warrant internal reporting to spot safety gaps before a serious injury occurs.
What are the penalties for lack of incident recording and reporting?
Up to $134,937 per violation. Knowingly providing false documentation carries criminal liability with massive fines and potential jail time.
What elements belong in an incident investigation?
Interviews with those involved, timestamped sequence of events, identification of root causes like poor training or complacency, photos of accident scene, relevant operating procedures.
What are some common corrective actions after an investigation?
Guard installation, PPE enhancements, fatigue management, safety committee formation, inspections, job hazard analysis refreshers, operating procedure updates, housekeeping improvements.
How can I encourage candid reporting in my shop?
Foster open culture for surfacing issues without blame before small risks become mass incidents. Reward speaking up. Offer anonymous reporting. Celebrate Good Catch near misses.
Call to Action
Rigorous reporting, timely investigation, transparent communications, and ongoing engagement between leadership and shop employees minimizes risk and enhances productivity in woodworking facilities.
Use this article as a jumping off point to review your safety incident management program. Brainstorm improvements harnessing the passion of your people to avoid preventable harm.
What safety practices have helped reduce close calls and minor cuts in your shop? Please share your experiences in the comments. Together we can build a community advancing safe woodworking across every project.